Rockflow Concrete
Rock Solid’s Rockflow is a highly fluid self compacting concrete which enables the quick and effortless pouring of slabs and floors whilst obtaining a high quality surface finish. It is intended for use in all types of unbonded, floating or bonded flooring applications. It can also be utilised in many screeding applications.
Key Benefits
- Quality Surface Finish – Rockflow enhanced finishing characteristics and high quality surface finish often mean the elimination of the use of power-floated concrete on site. Floor finish tolerance is to BS 8204 SR2=-/+ 5mm in 3m.
- Flexible Placing – Can be placed directly from the truck mixer chute, pump, or craned skip.
- Reduced Labour – Rockflow is convenient, saves time and permits the flexible use of labour on the building site.
- No Vibration – Placing Rockflow requires no vibration, eliminating the inherent problem of ‘vibration white finger’ and also gives reduced noise pollution.
- Application – Can be used typically in the following applications; slabs, structural toppings and oversite. Can also be used in screeding applications where a heavy duty or structural screed is required.
- Noise – Elimination of traditional methods of placing and finishing concrete or screed. Ideal when working in inner-city and built up residential areas.
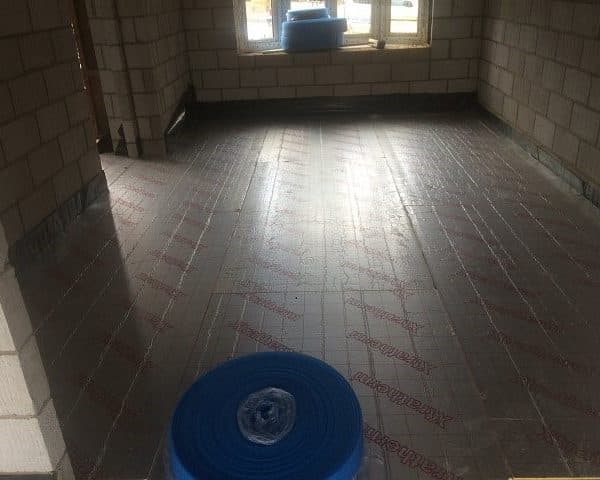
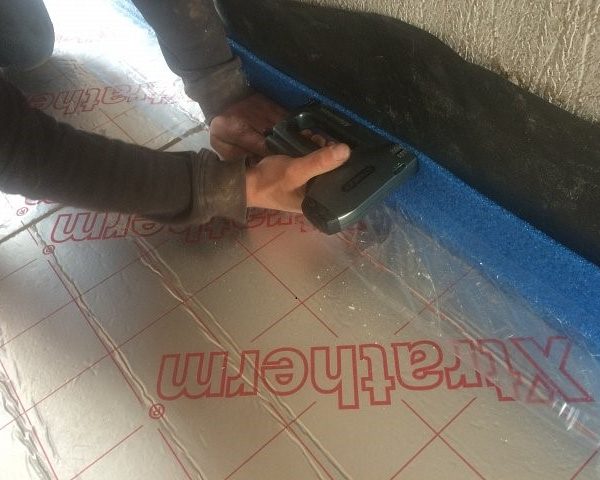
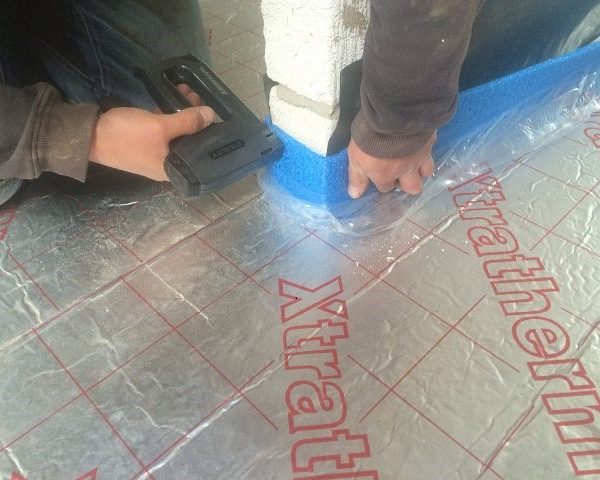
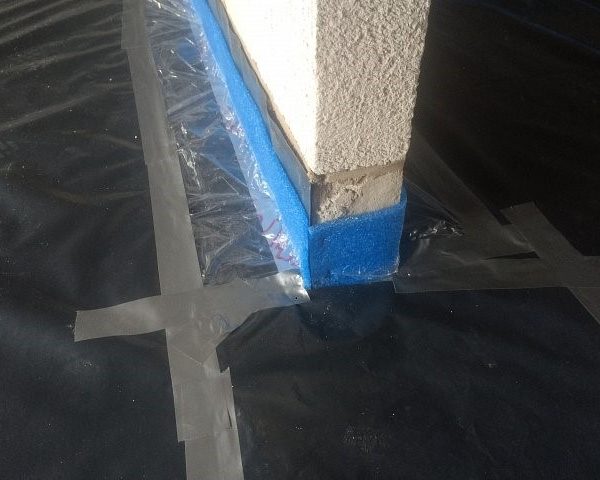
Rockflow – constituents and Design Project
The information detailed below relates to Rock Solid’s Rockflow. The main components and minimum performance characteristics are as follows:-
- Cement Type C111A in accordance with BS EN197
- Coarse Aggregates in accordance with BS EN12620.. 2002
- Fine Aggregates in accordance with BS EN12620..2002
- Admixtures in accordance with BS EN934
- Consistence Class 700-750 slump flow in accordance with BS EN 12350-8
- Maximum Water Cement Ratio: <0.45
- Minimum cement content: > 400kg/m3
- Minimum thickness = 75mm when used as a concrete or screed and over Under floor heating
- May contain micro Fibre in accordance with standard: EN 14889-2:2006 and issued Certificate No; 533591
Rockflow Typical Compressive Strengths are in excess of 35N/mm2 (or to customer’s specification) are typical at 28 days.
As with all concrete, an effective curing regime must be in place, typically using a sprayed, 90% efficient curing agent.
Rock Solid’s Rockflow is a high quality concrete product, which is designed, produced, transported and supplied in accordance with our IS0 9001:2000 third party accredited quality scheme (QSRMC) and in accordance with the relevant parts of BS8500 Part 2 and BS EN206 Part 1.
Rock Solid’s Rockflow – Frequently Asked Questions
- Do I have to powerfloat it?
No. The main reason for using Rock Solid’s Rockflow is to eliminate the need for this operation. - Do I have to vibrate it?
No. Rock Solid’s Rockflow is “self-compacting”, which means that you don’t have to vibrate it to compact it. - How do I finish it?
When Rock Solid’s Rockflow has been placed to the desired levels, it should be dappled (or tamped) by using an aluminium or steel T-bar. You should make two passes with the bar, the second being at right angles to the first. On the first pass the bar must be moved vigorously to create big waves in the concrete. This levels the concrete. The second pass is done lightly on the surface of the concrete to get a good surface finish. This process can take place up to two hours after the time of batching. A curing agent must be applied just after the second pass using a high quality sprayer. - Can you pump it?
Yes. Rock Solid’s Rockflow is ideal for placing by pump. - Why do you have to spray a curing agent on the finished concrete?
The curing agent has three main purposes. Firstly it is used to prevent plastic shrinkage cracking by preventing the evaporation of water from the surface of the concrete. Secondly, by stopping the evaporation of water from the surface you prevent dusting of the finished slab and finally good curing allows the slab to fully develop its potential strength. Care must be taken to ensure complete coverage of the slab with the curing agent as per the manufacturer’s recommendations. - What happens if you do not cure it?
The concrete will crack. Depending on the site conditions, the cracking can be from very light (2 or 3 cracks/100m3) to a “crazy paving” type effect. - When can I walk on / load the slab?
The surface of the slab will be suitable for light foot traffic after a maximum of 24 hours. For the loading period, if no particular strength at early age has been asked for, the strength gain will be the same as for an OPC based mix. - What placing methods can I use?
The three main placing methods are:
- With a concrete pump
- Straight from the mixer truck
- With a skip and a crane
- How many people will I need to lay it?
Depending on the volume of concrete, the area to be poured and the method of placing you will need between 1 and 5 people. - What preparation is required before pouring?
Rock Solid’s Rockflow when being laid un-bonded, is to be laid on top of a watertight membrane. A compressive strip with a minimum thickness of 5mm is also required, to be fixed around vertical features such as columns, pipes and walls. When laid bonded, a primer must be applied on the substrate and reinforcement mesh is also required. - Is the finished concrete suitable to lay carpet / tiles directly onto?
Yes. - Will the finished surface be dusty when it dries?
No. The surface of the concrete will be dust-free after the setting time is allowed. - Can I lay it to falls?
No. Rock Solid’s Rockflow can’t be laid to falls because of its very high fluidity. - What is the setting time?
Depending on the temperature, the concrete will start to set 3 – 6 hours after placing. - Do I need to put steel in the concrete?
It is recommended to put a reinforcement mesh in any horizontal application to have a good repartition of the stresses induced by the shrinkage, but in an unbonded application, this can be avoided by a good site preparation. Any bonded applications will need at least a reinforcement mesh. - Can I lay it bonded?
Yes. Please consult with your Rock Solid Concrete representative for further guidelines and advice. - Can I rework the surface if I need to?
Yes but ONLY if necessary. - Do I have to put construction joints in and if so at what sections?
Yes, you do have to consider construction joints. The area between the joints shall not exceed 100m2 and the longest side shall not exceed 15m. The length to width ratio shall not exceed 2:1. Normal concreting practice should always be followed. - What ambient conditions can I pour in?
You can pour Rock Solid’s Rockflow when the ambient temperature is between 5 and 30 ºC - How long does the concrete stay fluid?
Rock Solid’s Rockflow is normally designed for slump retention of 3 hours. That can be adjusted if necessary to customer requirements. - Can I leave it as a finished product?
Yes. - What type of surface finish did I obtain?
The quality of surface finish can be defined by 2 characteristics: its flatness and its smoothness. Rock Solid’s Rockflow is normally sold as “Equivalent to a power float finish” but it is not identical. It will normally be flatter than a powerfloat but not as smooth.
Health & Safety Data Sheet
Concrete
COMPOSITION / INFORMATION ON INGREDIENTS
Mixture of aggregates, cement, water, admixtures, and cement replacement materials.
HAZARDS IDENTIFICATION
Wet Concrete
Contact with eyes may cause severe irritation and/or Alkali burns.
Skin contact may result in irritant contact dermatitis and/or ulceration due to the combination of wetness, alkalinity and abrasiveness of the cement mixture.
Allergic Contact Dermatitis may be caused by individual sensitivity to chromium compounds, which occur in cement.
Dry Concrete
Inhalation of Silica particles in dust caused by cutting/surface treatment of hardened screed may cause respiratory damage.
FIRST AID MEASURES
Wet Concrete
Eye Contact: Irrigate eyes immediately with clean water for at least 10 minutes. Seek immediate medical attention.
Skin Contact: Wash thoroughly with clean water as soon as contamination occurs. Note: This includes contact through contaminated clothing.
Dry Concrete
Eye Contact: Irrigate eyes immediately with clean water. Seek medical attention.
Skin Contact: Wash thoroughly with clean water.
Ingestion: Drink plenty of water and seek medical attention.
FIRE FIGHTING MEASURES
No fire or explosive hazard.
ACCIDENTAL RELEASE MEASURES
Personal Protection: Avoid contact with skin or eyes.
Wear impervious protective clothing. Environmental Measures:
Prevent from entering water courses, Drains or Sewers.
Method of Cleaning: Any spillage should be recovered immediately while material is still plastic and area washed thoroughly if applicable.
HANDLING AND STORAGE
Wet Concrete
Avoid direct skin and eye contact. Do not sit/kneel on wet concrete.
Dry Concrete
Minimise creation of dust wherever possible.
Wear trousers and impervious safety boots.
EXPOSURE CONTROLS / PERSONAL PROTECTION
Wet Concrete
Hand Protection: Wear suitable impervious gloves. Eye protection: Suitable Eye protection is strongly recommended where there is a risk of accidental splashing. Skin protection: Long sleeved clothing, full-length
Dry Concrete
Occupational Exposure Standards (OES), or Maximum Exposure Limits (MEL), for inhalants and respirable dusts are set by the Health & Safety Commission.
These are published annually in HSE Guidance Note EH40. The following limits (8 hour time-weighted averages) are given in EH40/99.
Total Inhalable Dust 10mg/m3 OES
Respirable Dust 4 mg/m3 OES
Respirable Crystalline Silica 0.3mg/m3 MEL.
Engineering Control Measures: Containment and local exhaust ventilation where airborn dust is likely to reach exposure limits.
Respiratory Protection: Suitable respiratory protective equipment to HSE approved standard if engineering control measures are insufficient.
Hand Protection: Abrasive resistant gloves.
Eye Protection: Goggles to approved HSE Standard.
PHYSICAL & CHEMICAL PROPERTIES
Detailed properties vary according to specific mix however, all concretes are:
- Abrasive.
- Alkaline (typically pH value 10 – 14).
STABILITY AND REACTIVITY
No safety issues relating to stability and reactivity of product under normal conditions.
TOXICOLOGICAL INFORMATION
Wet Concrete
Eye Contact: May cause irritation or alkali burns.
Skin Contact: May cause alkali burns and acute allergic dermatitis in people sensitised to chromium compounds. Long term exposure may cause irritant contact dermatitis, which can lead to sensitisation of the skin to chromium compounds.
Dry Concrete
Eye Contact: May cause transient irritation.
Skin Contact: No harm likely.
Inhalation: Inhalation of large quantities of dust may cause lung damage and in extreme cases may lead to premature death.
Ingestion: No harm likely.
ECOLOGICAL INFORMATION
When used as intended no environmental impact is anticipated.
Do not allow material to enter Water courses, Drains or sewers.
DISPOSAL CONSIDERATIONS
Non-Hazardous. Disposal subjects to Local Authority requirements and regulations.
TRANSPORT INFORMATION
Special Carriage Precautions: Nil. No vehicle labelling required.
REGULATORY INFORMATION
Chemicals (Hazard Information and Packaging for Supply) Regulations 1997. Danger Classification: Irritant (+hazard symbol)
R38 – Irritating to skin
R41 – Risk of serious damage to eyes.
R43 – May cause sensitisation by skin contact.
FURTHER INFORMATION SOURCES:
Sika Health & Safety Department
Sika Limited
Watchmead
Welwyn Garden City
Hertfordshire
AL7 1BQ
Tel: (01707) 394444
Fax: (01707) 329129